Switching power supply constant power control overload protection circuit
The schematic diagram of the current-type flyback switching power supply controlled by UC3842 is shown in Figure 1. It uses a dual-loop control mode, one is a voltage outer loop that detects the output voltage, one is a current inner loop that detects the switching current, and parallel with the current inner loop is a cycle-by-cycle current limiting power limiting module. Uin is the DC voltage after full-bridge rectification in the full voltage range, and Uth corresponds to the limited power point of the PWM chip. Due to the action of Zener diode Z1, the voltage value of Uth is clamped at 1V, which limits the peak current of the inductor and thus achieves power limitation. When the output load reaches the power limit point, as the load current continues to increase, the output voltage will decrease and enter the constant power control phase; Since the auxiliary power supply voltage supplied to the control chip reflects the output voltage, when the output voltage is reduced to a certain level, the auxiliary power supply will not be able to maintain the normal power supply of the IC. The power supply will perform repeated shutdown and restart actions to enter the Hiccup-mode protection phase; After the load returns to normal, the power supply returns to normal operation. According to the above principle, the relationship between the output voltage and the output current of the constant power control overload protection circuit shown in FIG. 2 can be known.
It is worth noting that there is a transmission delay from the sampling of the switching current to the switching of the switch Q1. This includes the propagation delay of the control chip from the current sample input to the output (typically 150ns for the UC3842), the turn-off delay of the switch Q1, and the delay caused by the filter circuit used to eliminate the leading edge of the switch current. This delay time will make the low-voltage operation of the switching power supply operating at full voltage range (90~264Vac) inconsistent with the maximum power point of high-voltage operation. In practical applications, an input voltage compensation circuit needs to be added to compensate to reduce the difference between the maximum power point and the high input voltage and low input voltage. As shown in FIG. 1, the circuit compensates for the detected switching current signal by superimposing a DC component that varies with the input voltage through the compensation resistors RP and RS2. In practical applications, the value of RS2 is about 1k: to ensure that the value of RP is large enough to protect the control IC. The following describes the method of RP and RS1 in the case of discontinuous conduction mode (DCM) and continuous conduction mode (CCM). Figure 3 is a waveform diagram of the switching current after compensation in the two modes. Among them, Ith is the maximum current sampling input threshold of UC3842. The value is the ratio of Uth to the sense resistor RS1, ICL and ICH are the compensation currents at the low voltage and high voltage input, and td is the transmission delay from the switch current sampling input to the switch Q1. IPH is the peak value of the switching current at high input voltage, and IPL is the peak value of the switching current at low input voltage.
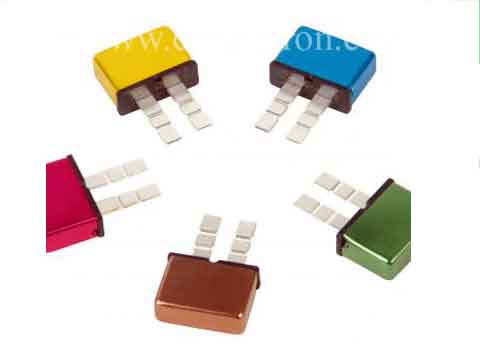
It is worth noting that there is a transmission delay from the sampling of the switching current to the switching of the switch Q1. This includes the propagation delay of the control chip from the current sample input to the output (typically 150ns for the UC3842), the turn-off delay of the switch Q1, and the delay caused by the filter circuit used to eliminate the leading edge of the switch current. This delay time will make the low-voltage operation of the switching power supply operating at full voltage range (90~264Vac) inconsistent with the maximum power point of high-voltage operation. In practical applications, an input voltage compensation circuit needs to be added to compensate to reduce the difference between the maximum power point and the high input voltage and low input voltage. As shown in FIG. 1, the circuit compensates for the detected switching current signal by superimposing a DC component that varies with the input voltage through the compensation resistors RP and RS2. In practical applications, the value of RS2 is about 1k: to ensure that the value of RP is large enough to protect the control IC. The following describes the method of RP and RS1 in the case of discontinuous conduction mode (DCM) and continuous conduction mode (CCM). Figure 3 is a waveform diagram of the switching current after compensation in the two modes. Among them, Ith is the maximum current sampling input threshold of UC3842. The value is the ratio of Uth to the sense resistor RS1, ICL and ICH are the compensation currents at the low voltage and high voltage input, and td is the transmission delay from the switch current sampling input to the switch Q1. IPH is the peak value of the switching current at high input voltage, and IPL is the peak value of the switching current at low input voltage.
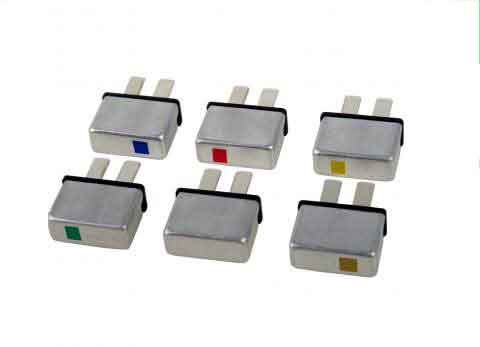