A Novel Single-Phase Motor Overcurrent Protector Design
When the motor is blocked, its working current Iw increases, and the voltage Vt increases. According to the above VO1, VO2 conduction function relationship, it can be concluded that VO2 also increases. Since the preset reference voltage Vref is constant, so that the increased VO2 is greater than Vref, the voltage comparator U3 turns on the output, the normally open contact of the relay K1 is closed, and the normally closed contact is opened. The normally open contact is connected to the control system for disconnecting the power supply circuit of the motor in time, and immediately emits an audible and visual alarm, thereby achieving overcurrent protection for the single-phase motor.
As can be seen from Figure 2. The overcurrent protector uses only a few inexpensive components such as diodes, op amps, voltage comparators, and some resistors to complete overcurrent protection for low-power single-phase motors. Moreover, the protection current is precisely adjustable, and the protection action speed is fast and accurate, which overcomes the drawbacks of the traditional bimetal thermal overload relay.
3, Component selection of the design scheme
The design of the electronic overcurrent protector requires a series of two (each set of 6) diodes D1 to D12 connected in series in the power supply loop of the single-phase motor. Without affecting the normal operation of the motor, a smaller AC power source (about AV 6V) is obtained for the overcurrent protector to work. The AC voltage is rectified and regulated to generate a DC 5V power supply to supply power to the entire circuit; The DC voltage across the current sampling resistor R0 is differentially amplified by the operational amplifier U2, amplified in the same phase, and then entered into the voltage comparator U3 and the preset reference voltage Vref for comparison and output to drive the relay K1. Since the rated operating current of the single-phase motor actually used by the author is about 0.2 to 0.5A, the designed overcurrent protector current setting value is between 0.2 and 1.2A and can be adjusted by the 5K potentiometer R10. According to the theoretical calculation and the actual experience of the author, the components in Figure 2 are selected as follows:
R0: 0.51Ω 5W 1%
R5, R6, R7, R8: 27K 1%
R9: 1K 1%
R10: 5K 3386 potentiometer
R11: 12K 1%
R1, R12, R13: 2.2K 5%
R4: 30K 1%
R2, R3: 20K 1%
C1: 10uF/25V
C2: 47uF/16V
C7: 100nF/50V
D1 to D12: S3N
B1: MB16S
U1: MIC39100-5.0BS
U2: LM358
U3: LM311
LED1: red LED tube
K1: G5V-2-H1-05V (Note: Omron, 2 normally open 2 normally closed relay)
In the above components, the current sampling resistor R0 is directly connected in series to the motor power supply circuit, so the plug-in resistor with power of 5 watts is selected. R10 selects 5K type 3386 adjustable potentiometer. Other resistors have no power requirement. You can choose the ordinary 0805 package chip resistance. Capacitors C1 and C2 select ordinary aluminum electrolytic capacitors, and capacitor C7 selects ordinary J-type magnetic capacitors; D1 to D12 select a rectifier diode S3N with an IF of 3A and a VF of 1.2V; B1 selects the Schottky rectifier bridge MB16S of the patch; Because the voltage before voltage regulation is only about 6V, so to get 5V voltage, U1 must have a voltage difference of less than 1V regulator, so I choose a low dropout regulator with a voltage difference of 410MV - MIC39100-5.0BS; U2 chooses the most commonly used operational amplifier on the market: LM358, low price, easy to buy; U3 selects the most common voltage comparator LM311 on the market, with open-drain output, which can directly drive the relay; K1 can select 2 normally open power type relays according to the actual contact capacity.
As can be seen from Figure 2. The overcurrent protector uses only a few inexpensive components such as diodes, op amps, voltage comparators, and some resistors to complete overcurrent protection for low-power single-phase motors. Moreover, the protection current is precisely adjustable, and the protection action speed is fast and accurate, which overcomes the drawbacks of the traditional bimetal thermal overload relay.
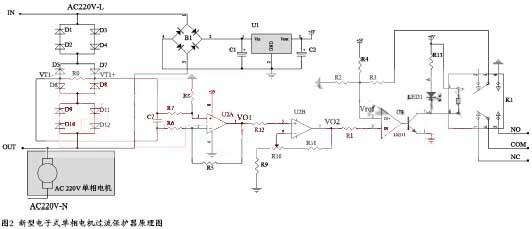
3, Component selection of the design scheme
The design of the electronic overcurrent protector requires a series of two (each set of 6) diodes D1 to D12 connected in series in the power supply loop of the single-phase motor. Without affecting the normal operation of the motor, a smaller AC power source (about AV 6V) is obtained for the overcurrent protector to work. The AC voltage is rectified and regulated to generate a DC 5V power supply to supply power to the entire circuit; The DC voltage across the current sampling resistor R0 is differentially amplified by the operational amplifier U2, amplified in the same phase, and then entered into the voltage comparator U3 and the preset reference voltage Vref for comparison and output to drive the relay K1. Since the rated operating current of the single-phase motor actually used by the author is about 0.2 to 0.5A, the designed overcurrent protector current setting value is between 0.2 and 1.2A and can be adjusted by the 5K potentiometer R10. According to the theoretical calculation and the actual experience of the author, the components in Figure 2 are selected as follows:
R0: 0.51Ω 5W 1%
R5, R6, R7, R8: 27K 1%
R9: 1K 1%
R10: 5K 3386 potentiometer
R11: 12K 1%
R1, R12, R13: 2.2K 5%
R4: 30K 1%
R2, R3: 20K 1%
C1: 10uF/25V
C2: 47uF/16V
C7: 100nF/50V
D1 to D12: S3N
B1: MB16S
U1: MIC39100-5.0BS
U2: LM358
U3: LM311
LED1: red LED tube
K1: G5V-2-H1-05V (Note: Omron, 2 normally open 2 normally closed relay)
In the above components, the current sampling resistor R0 is directly connected in series to the motor power supply circuit, so the plug-in resistor with power of 5 watts is selected. R10 selects 5K type 3386 adjustable potentiometer. Other resistors have no power requirement. You can choose the ordinary 0805 package chip resistance. Capacitors C1 and C2 select ordinary aluminum electrolytic capacitors, and capacitor C7 selects ordinary J-type magnetic capacitors; D1 to D12 select a rectifier diode S3N with an IF of 3A and a VF of 1.2V; B1 selects the Schottky rectifier bridge MB16S of the patch; Because the voltage before voltage regulation is only about 6V, so to get 5V voltage, U1 must have a voltage difference of less than 1V regulator, so I choose a low dropout regulator with a voltage difference of 410MV - MIC39100-5.0BS; U2 chooses the most commonly used operational amplifier on the market: LM358, low price, easy to buy; U3 selects the most common voltage comparator LM311 on the market, with open-drain output, which can directly drive the relay; K1 can select 2 normally open power type relays according to the actual contact capacity.