What is Thermal Overload Protector?
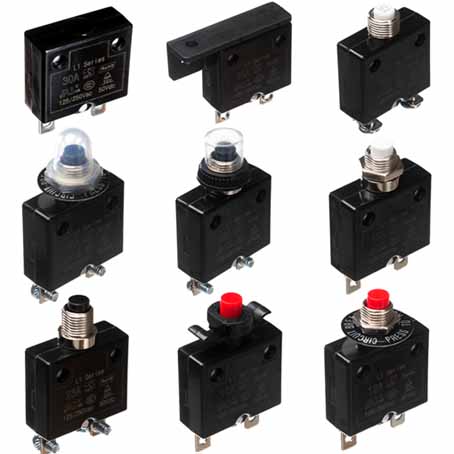
The thermal overload protector switch is an overload circuit breaker that uses the principle of current thermal effect and uses electrical and thermal bimetal as the sensitive element. Also known as recoverable overload switch and current overload protector. The thermal overload protector is easy to install and use, has complete functions and low purchase cost. The so-called electrical thermosensitive bimetallic sheet is heated and rolled by two alloys with a large difference in linear expansion coefficient. When heated, the bimetallic sheet bends from the high expansion layer (active layer) to the low expansion layer (passive layer). When the current is too large (exceeding the setting value), the element will act due to "heating". As a result, its linked movable-break contact cuts off the power supply of the controlled circuit and the protected equipment.
The thermal overload protector is used for the overload protection of the motor and the compressor, and there are many types. Practice has proved that it can reliably protect the motor, so it has always occupied an important position.
Working principle and purpose
The thermal element of the thermal overload protection switch is connected to the motor circuit directly or through a current transformer. When the motor is overloaded, the main bimetal is heated to the operating temperature, the overload protection switch is activated, and the power circuit of the motor is disconnected to prevent the motor from being damaged by the overload. The operating time of the thermal overload protector and the size of the overload current change in an inverse time limit. Therefore, its thermal characteristics are easily matched with the thermal characteristics of the motor, and it also has the characteristics of simple structure, low price, stable action performance, and convenient use. Therefore, most rotor motors and some wound rotor motors still use thermal overload protectors as protections for overload, phase failure and current unbalanced operation. The thermal over-protection switch can also be used to control the heating state of other electrical equipment.
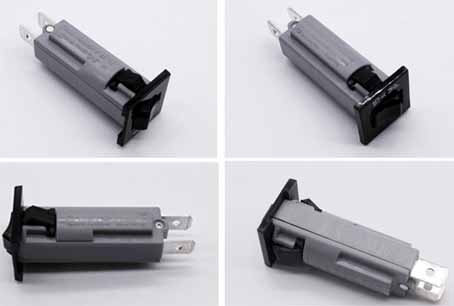
Application range of thermal overload protection switch: The thermal overload protection switch is used in circuits with AC 50Hz, rated insulation voltage of 660V, and current of 0.1~63A. Mainly used for overload and phase failure protection of single-phase and three-phase AC motors. It can also form a starter with an adapted AC contactor.
Structure
There is a current adjusting cam to adjust the set current.
There is a temperature compensation device to ensure that the operating characteristics are basically unchanged within the ambient medium temperature range of -20C to 60C.
There is a reset adjustment knob to adjust the reset mode: manual reset and automatic reset.
There is a tension spring flip and jump mechanism to ensure rapid and reliable contact action.
There are differential phase failure/single-phase/three-phase unbalance protection devices.
There is a detection slider/switch position indicator to simulate the trip of the thermal overload protection switch and display the action status. Check and ensure that the auxiliary circuit wiring is correct through this simulation method. When the marking on the slider is at the “0” mark, it shows tripping disconnection, and at the “l” mark, it shows power-on operation.
There is a disconnect button. When the disconnect button is pressed, the normally closed contact opens the series contactor and disconnects the load. After releasing the disconnect button, the load will work again through the contactor.
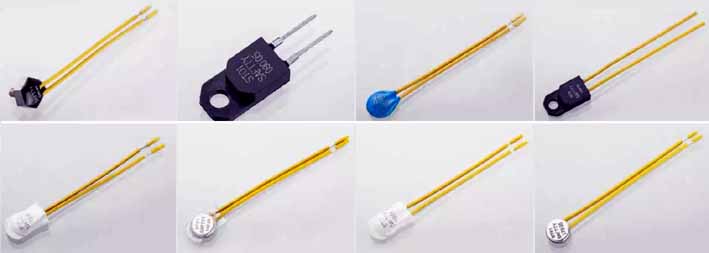
The overload protector can only be used as overload protection to control the motor, not as short-circuit protection.
The rated current of the protected object must be understood when installing, and the selection specification must be +20% of the rated current.
Usually installed directly after the starting contactor (Magnetic Switch) of the motor.
When the current is too high or the load current exceeds the setting, the overload protection switch will be activated and the circuit will be broken. Although the path can be restored by resetting the button, if the device overload protection switch is activated, the set current cannot be increased arbitrarily. The cause of the overload should be found out, otherwise the protected device will be easily burned.
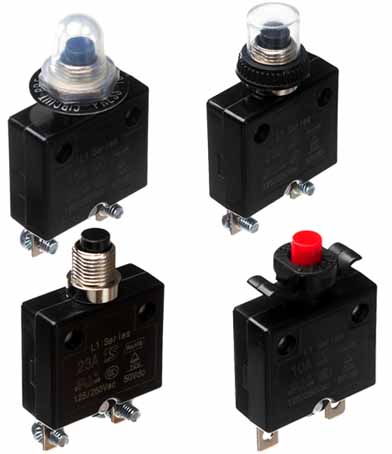
(1) Critical current:
Under the specified conditions, the thermal overload protection switch can operate with a current slightly larger than this value, and a current that cannot operate with a current slightly smaller than this value. It is the average value of the minimum operating current and the maximum non-operating current.
(2) Action characteristics:
The relationship between the operating time and the multiple of the overload current. Change according to the inverse time relationship, that is, the larger the overload current multiple, the shorter the action time. The action characteristic is also called the time-current characteristic.
(3) Cold action time:
Under the specified conditions, the time from when the overload current is applied to the thermal overload protection switch from the cold state to its action.
(4) Hot action time:
Under the specified conditions, the thermal overload protection switch is first applied with a preheating current (usually 1.0 or 1.05 times the setting current), after reaching thermal stability, then the overload current is applied to the time until its action. Obviously, under the same overload current multiple, the hot state action time is shorter than the cold state action time. Generally, the hot operating time is about 25% of the cold operating time.
(5) Temperature compensation:
Eliminate or reduce the effect of ambient air temperature changes on the operating characteristics of the thermal over-protection switch.
(6) The main bimetallic strip:
A bimetallic sheet that is heated and bent under overload current to cause the heat to overheat the protective switch to produce an action.
(7) Compensated bimetallic strip:
Feel the surrounding air temperature change and produce a bend to compensate for the surrounding air temperature change. Compensation of the effect of the main bimetallic strip on the performance of the bimetallic strip.