Motor protector working principle
The motor protector consists of a three-phase current transformer, detection, amplification, delay, adjustment circuit and execution relay. When the detection circuit detects that the current induced by the current transformer is out of phase or is greater than the set value, the amplifier is amplified to activate the relay. The relay contact is connected in series with the contactor coil power supply circuit, and the contactor is powered off after the relay acts to protect the motor. The delay circuit is used to avoid the starting current of the motor and its duration is adjustable. The adjustment circuit is used to accurately set the operating current according to the operating current of the protected motor.
The motor protector is a classic motor star-delta startup method, mainly to protect the thermal relay. If a large relay is used to protect a large motor, it will cause a breakpoint in the large wire, that is, a screw connection problem of entering and leaving the thermal relay, and it is prone to hot spots and fault points. If a fuse and a thermal relay are not used, a motor integrated protector is used. Because the protector is a core-through type, it can reduce the breakpoint of large wires, thus reducing the hot spots and fault points.
When using the motor protector, you must pay attention to the wiring problem of the control circuit to ensure the normal operation of the machine. It can replace a product of low-voltage electrical appliances such as circuit breakers, contactors, thermal relays, and fuses.
Motor protector protection principle
The main cause of motor burnout is phase failure and overload burnout of the windings during operation. Therefore, the circuit with the motor should be equipped with a motor protector to ensure that the working power is cut off in time when the motor is out of phase and overcurrent, and the motor is protected from damage. The main protector for small motors is the thermal relay. When faced with a large motor, if the motor is also protected by a thermal relay, the connection point (ie, the screw connection point to and from the thermal relay) is prone to heat generation and failure to avoid the above problem. There is a motor integrated protector, the motor integrated protector is a heart-through type, can be less wire connection points, can reduce the heat point and the point of failure is also cheap. When using the motor integrated protector, you must pay attention to the wiring problem of the control circuit to ensure normal operation.
Some large motor cooling system failures or long-term operation in high temperature and high humidity environment cause motor failure. Research on the principle of motor protection is the key to ensuring the performance of the motor protector. According to the theory of three-phase symmetrical component method, three asymmetric vectors can be uniquely decomposed into three sets of symmetric vectors, which are positive sequence component, negative sequence component and zero sequence component. When the motor is symmetrical and asymmetrical, the three-phase current of the motor changes. Motor fault conditions The current flowing through the windings is too large to exceed the rated current of the motor, so the motor overcurrent can be protected according to this feature. Motor overload, phase failure, and undervoltage will cause the winding current to exceed the rated value. When the power supply voltage is under voltage, the ratio of the rising current of the running current will be equal to the ratio of the voltage drop; when the motor is overloaded, it often causes the stalling, and the running current at this time will greatly exceed the rated current. In view of the above situation, the motor protector can detect the three-phase running current and determine different protection modes according to different properties of the running current, thereby providing power-off protection to the motor.
The motor protector is a classic motor star-delta startup method, mainly to protect the thermal relay. If a large relay is used to protect a large motor, it will cause a breakpoint in the large wire, that is, a screw connection problem of entering and leaving the thermal relay, and it is prone to hot spots and fault points. If a fuse and a thermal relay are not used, a motor integrated protector is used. Because the protector is a core-through type, it can reduce the breakpoint of large wires, thus reducing the hot spots and fault points.
When using the motor protector, you must pay attention to the wiring problem of the control circuit to ensure the normal operation of the machine. It can replace a product of low-voltage electrical appliances such as circuit breakers, contactors, thermal relays, and fuses.
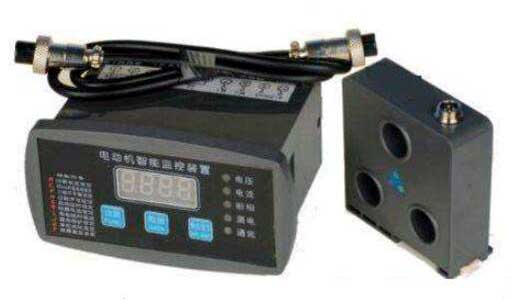
Motor protector protection principle
The main cause of motor burnout is phase failure and overload burnout of the windings during operation. Therefore, the circuit with the motor should be equipped with a motor protector to ensure that the working power is cut off in time when the motor is out of phase and overcurrent, and the motor is protected from damage. The main protector for small motors is the thermal relay. When faced with a large motor, if the motor is also protected by a thermal relay, the connection point (ie, the screw connection point to and from the thermal relay) is prone to heat generation and failure to avoid the above problem. There is a motor integrated protector, the motor integrated protector is a heart-through type, can be less wire connection points, can reduce the heat point and the point of failure is also cheap. When using the motor integrated protector, you must pay attention to the wiring problem of the control circuit to ensure normal operation.
Some large motor cooling system failures or long-term operation in high temperature and high humidity environment cause motor failure. Research on the principle of motor protection is the key to ensuring the performance of the motor protector. According to the theory of three-phase symmetrical component method, three asymmetric vectors can be uniquely decomposed into three sets of symmetric vectors, which are positive sequence component, negative sequence component and zero sequence component. When the motor is symmetrical and asymmetrical, the three-phase current of the motor changes. Motor fault conditions The current flowing through the windings is too large to exceed the rated current of the motor, so the motor overcurrent can be protected according to this feature. Motor overload, phase failure, and undervoltage will cause the winding current to exceed the rated value. When the power supply voltage is under voltage, the ratio of the rising current of the running current will be equal to the ratio of the voltage drop; when the motor is overloaded, it often causes the stalling, and the running current at this time will greatly exceed the rated current. In view of the above situation, the motor protector can detect the three-phase running current and determine different protection modes according to different properties of the running current, thereby providing power-off protection to the motor.