Based on SCR Hall element circuit overcurrent and overload protection
Its basic working principle is that a closed magnetic circuit with a certain gap is composed of two U-shaped magnets and two three-terminal integrated Hall elements. As a current detection system, a load and a thyristor current wire pass through the center of the magnetic circuit plane to generate an alternating magnetic field in the magnetic circuit, as shown in FIG. When the current value of the thyristor is within the rated range, the magnetic field strength generated in the magnetic circuit is small, lower than the operating magnetic field strength of the Hall element, and the protection circuit does not operate. In the event of an overcurrent condition, the strength of the magnetic field will increase, which will exceed the operating strength of the Hall element, and the Hall element will be triggered to flip and also trigger the protection circuit. It turns off the trigger circuit of the main circuit thyristor and turns off the thyristor after zero crossing.
IC1 and IC2 in the circuit are Hall IC ULN3020. In normal working conditions, their output terminal feet are always low level. D2, D3 cut off, the thyristor T1 is also in the off state, the luminous tube L4 does not emit light, and the positive power supply forms a loop through R6, L1, IC4, R5, VT to the ground. If the base of the control switch transistor VT is extremely high, it will be in a conducting state. Thus, the zero-crossing flip-flop IC4 is turned on, triggering the bidirectional silicon T3 to conduct, and the load RL is electrically operated, and their current will generate an alternating magnetic field in the magnetic circuit. When the peak of the magnetic field strength does not reach the opening magnetic field strength of the two Hall elements, both IC1 and IC2 remain unchanged. When the current abnormally increases due to abnormal load or other reasons, one of IC1 and IC2 will be in a short-time high output state. Thus, the thyristor T1 is turned on by D2 or D3, and D5 is turned on, so that the zero-crossing flip-flop IC4 is turned off, and the thyristor T3 is turned off after the power supply is zero-crossed. At the same time, the light-emitting tube L4 is lit, D4 is also turned on, and the buzzer BU emits an alarm sound, and the thyristor T1 can be kept in an on state until the power of the control circuit is turned off.
There is also a set of thyristor overheat protection circuits in this circuit. IC3 is a TO-220 package type 67L070 two-leg temperature sensing switch element, its operating temperature is 70 ° C, in the normal temperature state is normally closed. It is mounted on the heat sink of the thyristor T3. When the thyristor is overloaded or otherwise, the power consumption is greatly increased. Once the temperature of the heat sink reaches 70 °C, IC3 will change from normally closed to normally open. At this time, T2 will be turned on by R10, and D6 will also be turned on, which will cut off IC4 and cut off the thyristor T3. At the same time, D7 is also turned on, the light-emitting tube L3 is lit, D6 is turned on, the buzzer BU is working, and an alarm sound is issued. The thyristor T2 can also remain in a conducting state at all times. Finally, until the control power is turned off.
The magnitude of the current that causes the Hall element to operate can be determined by adjusting the spacing between the two U-shaped cores. For the 40A thyristor used in this circuit, the maximum current through it should be limited to less than 40A. The core cross section used here is 5 mm * 4 mm, and the interval between the two cores is about 2.0 mm. However, due to the difference in magnetic permeability of different magnetic materials and the difference in parameters of the Hall elements, the specific intervals may be slightly different. The actual protection current is preferably determined by actual measurement and sealed on the printed board with glue. The requirement for the installation of two Hall components is that for the cross section of the magnetic body, the printing is all oriented in one direction. Only in this way can the two Hall elements detect the positive and negative half cycles of the AC current.
For further protection, a 32A air switch is also provided in the main circuit, which also functions to protect the thyristor and also serves as a control switch for the main circuit.
The shortcoming of this protection circuit is that when the load and the circuit are severely short-circuited, the protection effect on the thyristor is slightly insufficient. Because there have been cases where the thyristor is short-circuited, this is mainly because after the protection circuit operates, the thyristor can only be naturally turned off after the power supply has passed zero. The breaking speed of the air switch is also limited. Therefore, if necessary, other measures such as fast-melting should be used for the final short-circuit protection.
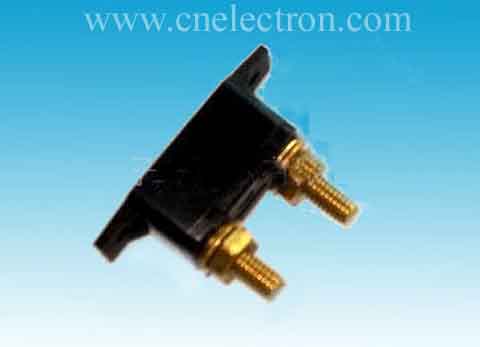
IC1 and IC2 in the circuit are Hall IC ULN3020. In normal working conditions, their output terminal feet are always low level. D2, D3 cut off, the thyristor T1 is also in the off state, the luminous tube L4 does not emit light, and the positive power supply forms a loop through R6, L1, IC4, R5, VT to the ground. If the base of the control switch transistor VT is extremely high, it will be in a conducting state. Thus, the zero-crossing flip-flop IC4 is turned on, triggering the bidirectional silicon T3 to conduct, and the load RL is electrically operated, and their current will generate an alternating magnetic field in the magnetic circuit. When the peak of the magnetic field strength does not reach the opening magnetic field strength of the two Hall elements, both IC1 and IC2 remain unchanged. When the current abnormally increases due to abnormal load or other reasons, one of IC1 and IC2 will be in a short-time high output state. Thus, the thyristor T1 is turned on by D2 or D3, and D5 is turned on, so that the zero-crossing flip-flop IC4 is turned off, and the thyristor T3 is turned off after the power supply is zero-crossed. At the same time, the light-emitting tube L4 is lit, D4 is also turned on, and the buzzer BU emits an alarm sound, and the thyristor T1 can be kept in an on state until the power of the control circuit is turned off.
There is also a set of thyristor overheat protection circuits in this circuit. IC3 is a TO-220 package type 67L070 two-leg temperature sensing switch element, its operating temperature is 70 ° C, in the normal temperature state is normally closed. It is mounted on the heat sink of the thyristor T3. When the thyristor is overloaded or otherwise, the power consumption is greatly increased. Once the temperature of the heat sink reaches 70 °C, IC3 will change from normally closed to normally open. At this time, T2 will be turned on by R10, and D6 will also be turned on, which will cut off IC4 and cut off the thyristor T3. At the same time, D7 is also turned on, the light-emitting tube L3 is lit, D6 is turned on, the buzzer BU is working, and an alarm sound is issued. The thyristor T2 can also remain in a conducting state at all times. Finally, until the control power is turned off.
The magnitude of the current that causes the Hall element to operate can be determined by adjusting the spacing between the two U-shaped cores. For the 40A thyristor used in this circuit, the maximum current through it should be limited to less than 40A. The core cross section used here is 5 mm * 4 mm, and the interval between the two cores is about 2.0 mm. However, due to the difference in magnetic permeability of different magnetic materials and the difference in parameters of the Hall elements, the specific intervals may be slightly different. The actual protection current is preferably determined by actual measurement and sealed on the printed board with glue. The requirement for the installation of two Hall components is that for the cross section of the magnetic body, the printing is all oriented in one direction. Only in this way can the two Hall elements detect the positive and negative half cycles of the AC current.
For further protection, a 32A air switch is also provided in the main circuit, which also functions to protect the thyristor and also serves as a control switch for the main circuit.
The shortcoming of this protection circuit is that when the load and the circuit are severely short-circuited, the protection effect on the thyristor is slightly insufficient. Because there have been cases where the thyristor is short-circuited, this is mainly because after the protection circuit operates, the thyristor can only be naturally turned off after the power supply has passed zero. The breaking speed of the air switch is also limited. Therefore, if necessary, other measures such as fast-melting should be used for the final short-circuit protection.